S’appuyant sur un principe d’acheminement des produits de la commande jusqu’à l’opérateur positionné sur un poste fixe, ce procédé dénote des solutions plus classiques où on demande aux préparateurs de se déplacer dans l’entrepôt pour récolter les différents articles à préparer. En complément de la multiplication de la performance des opérations de préparation détail, ces technologies permettent également de stocker temporairement les colis finalisés, avant palettisation et chargement, permettant ainsi une utilisation optimale du système.
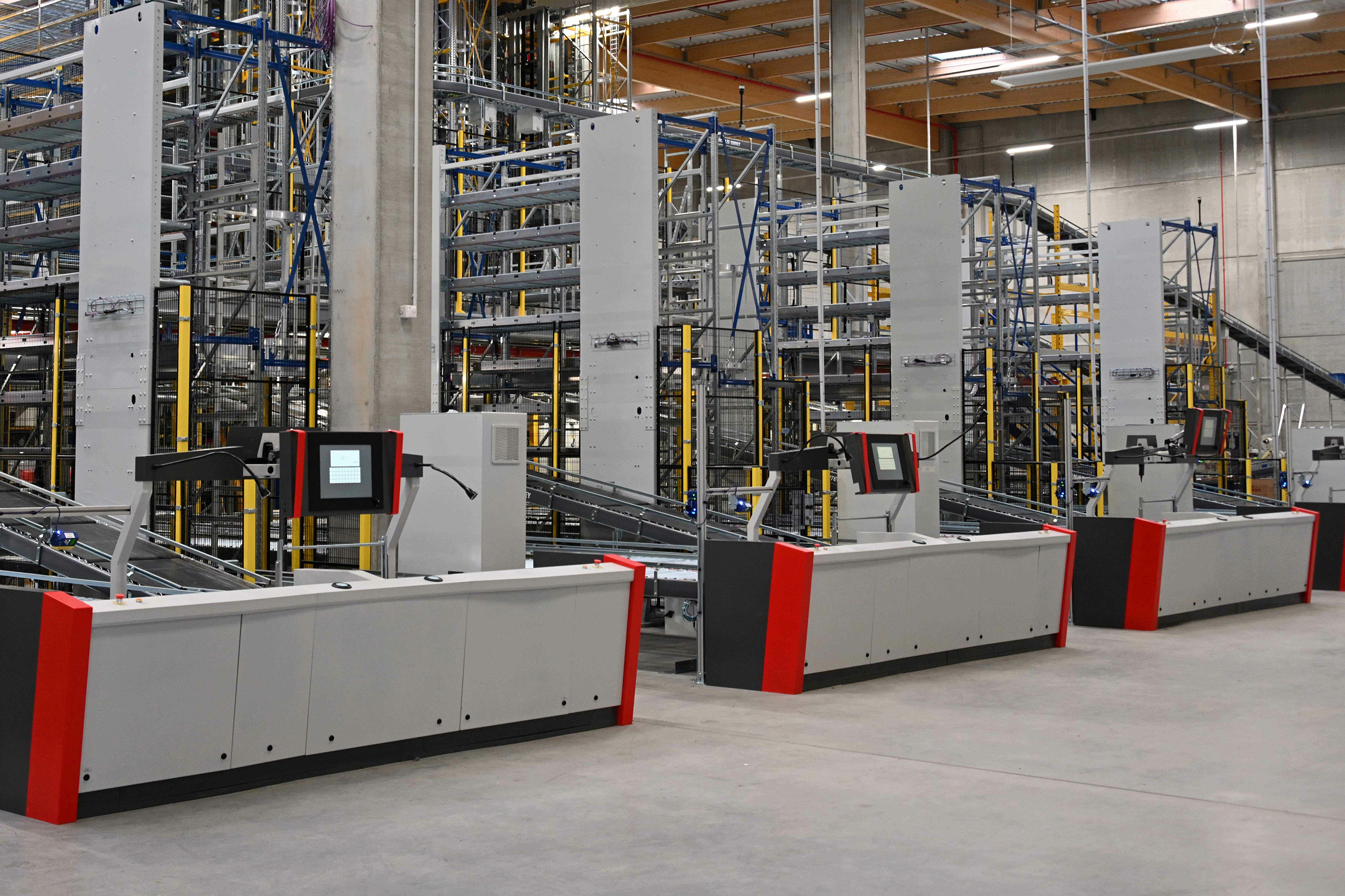
Systèmes Goods-to-Person : quels critères de comparaison ?
Les avancées technologiques de ces dernières années ont largement bénéficié à l’amélioration de la performance de la préparation de commandes. Parmi ces grandes avancées, les systèmes de préparation Goods-to-Person se démocratisent et deviennent un « must have » pour les entrepôts à la recherche de performance, d’une meilleure qualité de préparation mais aussi de réduction de la pénibilité pour les opérateurs.
DE NOMBREUX SYSTÈMES EXISTENT, QUELS-SONT-ILS ?
De nombreuses solutions Goods-To-Person existent ; les principales différences qui distinguent ces solutions résident dans les typologies d’équipements utilisés sur chaque axe dimensionnel (horizontal, vertical) pour réaliser les mouvements entre le stock et les postes de préparation. Si un seul équipement réalise les opérations, le point fort du système sera sa flexibilité. A l’inverse, plus les équipements seront dédiés à un axe, plus le système sera réactif et performant. Ces solutions peuvent être catégorisées par une grande typologie de famille.
Système à navettes/shuttle
l’espace de stockage est subdivisé en différents niveaux, auxquels sont associés des navettes réalisant les mouvements de prise et dépose sur l’axe horizontal. Sur l’axe vertical, des élévateurs assurent les entrées et sorties de supports.
Robots mobiles 2 ou 3 dimensions
généralement composé de bacs monoformat, le système de stockage est desservi par des robots mobiles capables d’évoluer sur 2 voire 3 axes pour apporter les produits jusqu’aux postes de préparation.
Miniload
un miniload est constitué d’un mât se déplaçant horizontalement et transportant verticalement un préhenseur, permettant ainsi d’accéder à l’ensemble des positions d’une même allée de stockage.
Armoires verticales
doté d’un système de stockage vertical et automatisé, comparable à une tour, cette solution est équipée de plateaux sur lesquels sont stockés les supports.
Robots mobiles étagères
l’espace de stockage est constitué d’étagères transportées par des robots mobiles jusqu’aux postes de préparation pour un prélèvement direct.
COMPARER LES SYSTÈMES : SELON QUELS CRITÈRES ?
La réactivité
C’est-à-dire la capacité du système à préparer une commande dans un temps réduit. En fonction des systèmes, la réactivité peut largement varier depuis quelques minutes à 1 heure. L’utilisation des axes est un point déterminant pour évaluer la réactivité du système. Le fonctionnement en batch, le fait de préparer les commandes en deux étapes, l’utilisation de technologies travaillant sur plusieurs axes à la fois ou encore le risque de congestion lié aux technologies de robots mobiles, sont autant de facteurs venant pénaliser la réactivité du système.
La densité volumique
C’est-à-dire l’utilisation qui est faite du volume disponible dans l’entrepôt (en moyenne 10 à 12m de hauteur). Le système Goods-To-Person est composé d’un espace de stockage qui se doit d’être plus compact que ceux des entrepôts travaillant en mode manuel. En effet, une des promesses de gain de ce système réside dans l’augmentation de la surface de stockage et le gain de place. Il faudra donc prendre en considération la réalité de ce gain dans l’entame d’une démarche comparative. Le système utilise-t-il toute la surface et tout le volume disponibles? Exploite-t-il tous les axes à sa disposition ? La circulation des supports est-elle optimisée pour éviter tout risque d’embouteillage ou d’engorgement ?
L’optimum économique
C’est-à-dire la rentabilité du système par rapport à l’usage et à la typologie d’activité pour laquelle il sera employé. Cet optimum économique varie fortement en fonction tout d’abord du volume de stockage nécessaire, exprimé en nombre de positions et également du flux maximal ciblé exprimé en lignes de commandes par heure. Le rapport entre ces deux valeurs permet assez rapidement de cibler la technologie adaptée c’est à dire celle apportant le meilleur optimum économique.
QUELLES TECHNOLOGIES POUR RÉPONDRE AUX ENJEUX DE PERFORMANCE ET DE RÉACTIVITÉ ?
Pour simplifier la comparaison, faisons le parallèle avec les moyens de transport. Dans les deux cas, il s’agit de transporter à destination, ou vers des stations de préparation de commandes, une certaine quantité de personnes, ou de supports, à une certaine vitesse. Chaque moyen de transport se caractérise par la vitesse maximale qu’il peut atteindre et par le nombre de passagers qu’il peut embarquer.
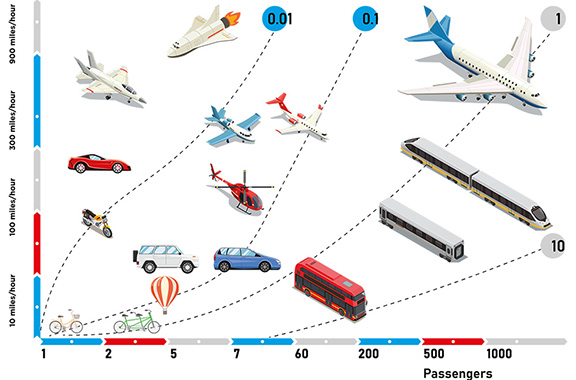
Comme le symbolise ce schéma, un vélo peut transporter 1 personne à une vitesse comprise entre 0 et 50km/h, tandis qu’une voiture pourra déplacer 4 à 5 personnes à une vitesse maximale de 130km/h. Enfin, le TGV, quant à lui, peut transporter 500 passagers à 300km/h.
En disposant ces informations sur le schéma, les moyens de transport peuvent ainsi être classés selon un critère d’efficacité obtenu par la division du nombre de passagers par la vitesse à laquelle on souhaite les transporter. Ce calcul permet d’obtenir un ratio qui varie sur ce schéma de 0,01 à 10 correspondant au nombre de personnes par heure et par kilomètre qu’il est possible de transporter. Chaque moyen de transport a ainsi sa propre zone de pertinence, représentant un optimum en fonction des besoins en vitesse et en nombre de personnes transportées.
Il n’existe pas de solution universelle : la visualisation des zones de pertinence permet de comparer les systèmes en termes d’efficacité et d’investissement.
La préparation de commandes robotisée Goods-To-Person répond à ces mêmes règles : il s’agit d’amener une certaine quantité de produits à une destination spécifique, à une certaine vitesse. Le calcul du facteur d’efficacité prendra en compte, en remplacement du nombre de passagers, la donnée du nombre de supports, qui peut contenir plusieurs références articles, et les mouvements de ces supports, en remplacement de la vitesse.
Ou, dit autrement, le rapport entre le nombre de lignes à préparer et le nombre de références disponibles dans le système.
Nous constatons sur le schéma ci-dessous que plusieurs solutions peuvent être retenues à iso-volume de stockage nécessaire. Tout dépend du flux attendu en préparation. Prenons l’exemple d’un système constitué de 15000 références à stocker. Si le flux nécessaire est de l’ordre de 500 lignes de commandes par heure, une solution à base de robots mobiles (type HAIPICK) représente l’optimum économique. Par contre si le flux attendu est de 1000 lignes de commande par heure, un système à navettes (type X-PTS) représente la meilleure alternative.
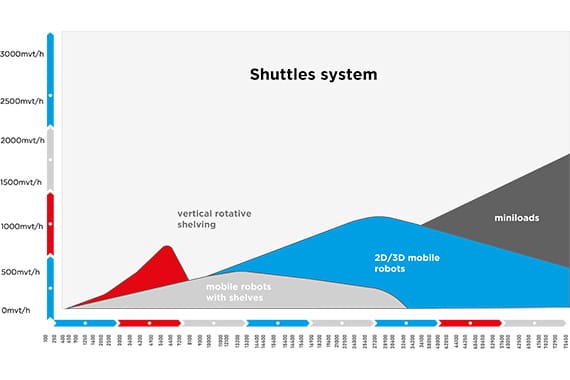
Autre exemple: pour un besoin de stockage de 8000 références et un flux de 300 lignes de commande par heure, une solution robot mobile étagère est idéale. En revanche, si le flux augmente au-dessus de 600 lignes par heure, un système à navettes est nettement plus avantageux.
Dernier exemple : pour un stockage très important, à partir de 50000 références et un flux réduit, autour de 1000 lignes par heure, une technologie traditionnelle à base de miniloads représente l’option la plus efficace et la plus économique.
Il n’y a donc pas de technologie universelle plus intéressante quel que soit le contexte, mais des zones de pertinence propres à chacune des solutions Goods-to-Person.
POUR CONCLURE...
Pour conclure, le parallèle réalisé avec les moyens de transport permet de bien comprendre l’importance d’évaluer l’efficacité mais aussi la rentabilité des différents systèmes Goods-To-Person en fonction de leur usage et de leur activité.
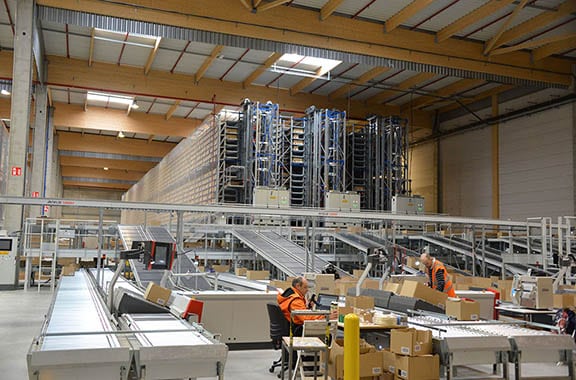
Il sera toujours possible de faire parcourir 600km à vélo à 600 personnes. Cependant, cela ne sera ni rapide, ni efficace. D’un autre côté, transporter 5 personnes par avion pour parcourir 200km est rapide et efficace, mais certainement pas rentable.
L’objectif de l’exercice de comparaison est donc de réussir à répondre favorablement à ces 3 aspects que sont la rapidité, l’efficacité et la rentabilité. Comme nous avons pu le constater, il existe plusieurs technologies sur le marché avec chacune leur zone de pertinence du point de vue réactivité, optimisation volumique, nombre de références à traiter et nombre de lignes de commandes à produire.
Dans le cadre d’un projet de consultation pour l’acquisition de ce type de solution, l’exploitant ou le cabinet conseil qui l’accompagne devra s’assurer de l’alignement du choix avec des critères d’analyse rationnels, garantissant l’adéquation de la solution avec le contexte de l’activité mais surtout le ROI du système.
Systèmes Goods-to-Person : quels critères de comparaison ?
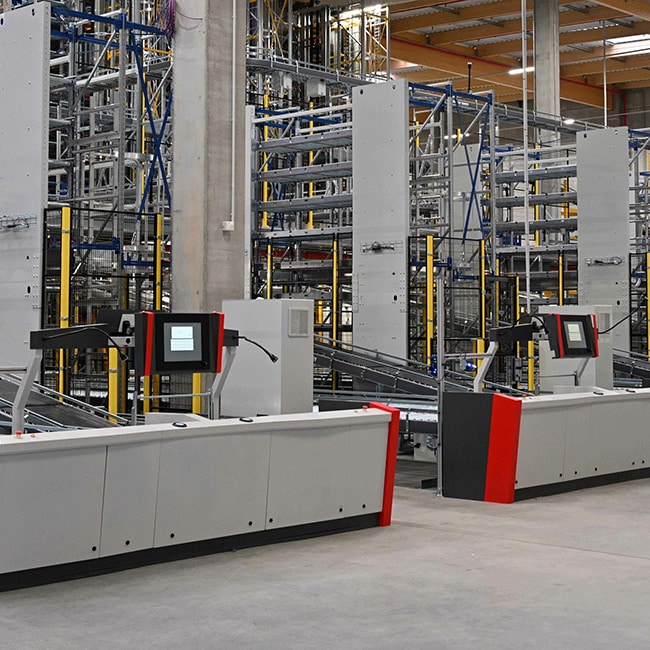