Based on the principle of conveying the products of an order to the operator at a fixed workstation, this process sets itself apart from more classic solutions that require the order pickers to move around the warehouse to collect the different items to be picked. In addition to the increased performance of retail picking operations, these technologies also make it possible to temporarily store finished packets, before being palletized and loaded, enabling optimal use of the system.
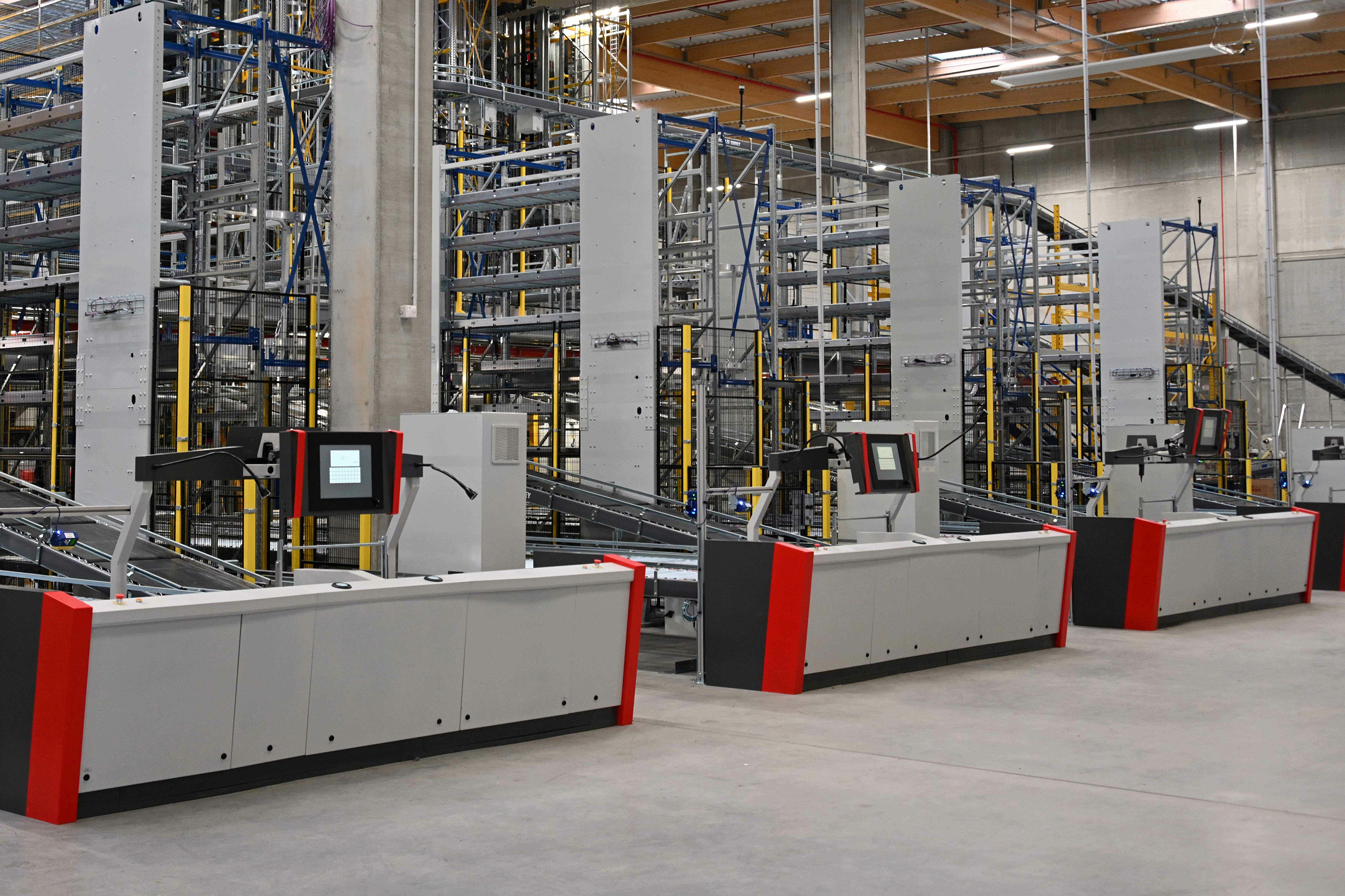
Goods-to-Person systems: how to compare them efficiently?
Technological advances over the past few years have largely led to improved performance in order picking. Among these major advances, goods-to-person picking systems are becoming more widespread and a must-have for warehouses looking for performance, better picking quality and reduced fatigue for operators.
VARIOUS DIFFERENT SYSTEMS EXIST: WHAT ARE THEY?
Different Goods-To-Person systems exist and we have seen that the offer is becoming increasingly more diverse. The main difference that set these solutions apart are the types of equipment used on each dimensional axis (horizontal, vertical) to move between the stock and the picking stations. If a single piece of equipment performs the operations, the major advantage of the system will be its flexibility. Conversely, if the equipment is dedicated to a single axis, the system will have better performance. Depending on these criteria, these solutions may be classified into different families
Shuttle system
the storage area is subdivided into different levels, which are linked to shuttles that carry out the pick-up and drop-off movements on the horizontal axis. On the vertical axis, elevators ensure the input and output of the carriers.
2 or 3-dimension mobile robots
generally made up of mono-format trays, the storage system is served by mobile robots able to move on 2 or 3 axes to bring the products right to the picking stations.
Miniload
a miniload moves horizontally and transports a LHD vertically, making it possible to access all the positions in the same storage aisle.
Vertical racks
equipped with a vertical and automated storage system, that can be compared to a tower, this solution is equipped with totes.
Mobile robot shelves
the storage area is made up of shelves transported by mobile robots to the picking stations for direct picking.
WHAT ARE THE BENEFITS OF SUCH A SOLUTION?
Responsiveness
i.e. the system’s ability to prepare an order in minimal time. Depending on these systems, responsiveness may vary from a few minutes to an hour. Using axes is also a crucial point to bear in mind when assessing the system’s responsiveness. Batch operation, i.e. picking orders in two steps, or using technologies that operate on several axes at the same time (congestion risk) are factors that may have a negative impact on the system’s responsiveness.
Volume density
i.e. the use that is made of the volume available in the warehouse (on average 10 to 12 m/33 to 39 ft. high). A Goods-To-Person system comprises a storage area that has to be more advantageous than those in warehouses that operate manually. Indeed, one of the major advantages of this system is the increase in storage surface area as well as saving space. This advantage must be considered when comparing different systems. Does the system make efficient use of the entire space? Does it operate on all the axes available? Is the moving of the carriers optimized to prevent any risk of congestion or clogging?
Economic optimum
i.e. the profitability of the system depending on the use or type of activity for which it will be used. This economic optimum varies widely depending on the required storage volume, expressed in number of positions and the target maximum flow expressed in order lines per hour. The ratio between both values makes it possible to quickly figure out which technology is best suited, i.e. the technology that will have the best economic optimum.
WHAT TECHNOLOGIES ARE THERE TO MEET THE CHALLENGES OF PERFORMANCE AND RESPONSIVENESS?
As this diagram shows, a bike can transport 1 person at a speed of between 0 and 50 km/h (approx. 30 mph), whereas a car can transport 4 to 5 people at a maximum speed of 150 km/h (approx. 90 mph). Finally, a high-speed train can transport 500 passengers at 300 km/h (approx. 190 mph).
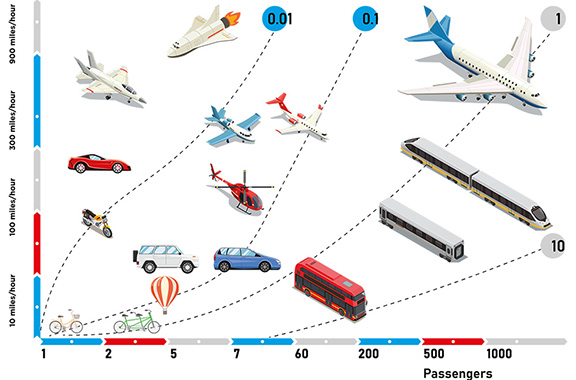
The same rules also apply to robotic Goods-To-Person order picking: a certain quantity of products have to be conveyed to a specific destination, at a certain speed. Calculating the efficiency factor will consider, instead of the number of passengers, the number of carriers (which may contain several items) and the movement of these carriers (instead of the speed in the previous calculation).
Or, in other words, the ratio between the number of lines to be picked and the number of product references available in the system.
As this diagram shows, a bike can transport 1 person at a speed of between 0 and 50 km/h (approx. 30 mph), whereas a car can transport 4 to 5 people at a maximum speed of 150 km/h (approx. 90 mph). Finally, a high-speed train can transport 500 passengers at 300 km/h (approx. 190 mph).
By outlining this information in the diagram, the different means of transport can be classified using an efficiency criterion obtained by dividing the number of passengers by the speed at which we would like to transport them. This calculation results in a factor that, for this diagram, varies between 0.01 and 10, corresponding to the number of people per hour and per kilometer/mile that we can transport. We can, therefore, compare these systems in terms of efficiency and investment.
The same rules also apply to robotic Goods-To-Person order picking: a certain quantity of products have to be conveyed to a specific destination, at a certain speed. Calculating the efficiency factor will consider, instead of the number of passengers, the number of carriers (which may contain several items) and the movement of these carriers (instead of the speed in the previous calculation).
Or, in other words, the ratio between the number of lines to be picked and the number of product references available in the system.
We can see on the diagram below that different solutions may be selected for the same required storage volume. It all depends on the picking flow. Let’s use the example of a system with 15,000 product references to be stored. If the required flow is around 500 order lines per hour, a solution based on mobile robots (such as HAIPICK) achieves the economic optimum. However, if the picking requirement increases to 1000 order lines per hour, a shuttle system (such as X-PTS®) is the best alternative.
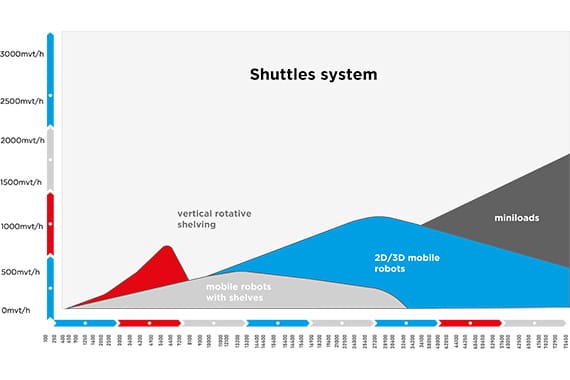
Another example: for a storage requirement of 8000 references and a flow of 300 order line items per hour, a mobile robot shelf solution is ideal. If the flow increases above 600 line items per hour however, a shuttle system is much more advantageous.
Last example: for a very large storage, from 50,000 references: and a reduced flow, around 1000 line items per hour, a traditional technology based on miniloads represents the most efficient and economical option.
Therefore, there is no universal technology that is superior in all situations, but areas of relevance specific to each of the Goods-to-Person solutions.
CONCLUSION...
In conclusion, the comparison made with transport demonstrates that it is extremely important to assess both the efficiency and profitability of the various Goods-To-Person systems depending on their use and activity.
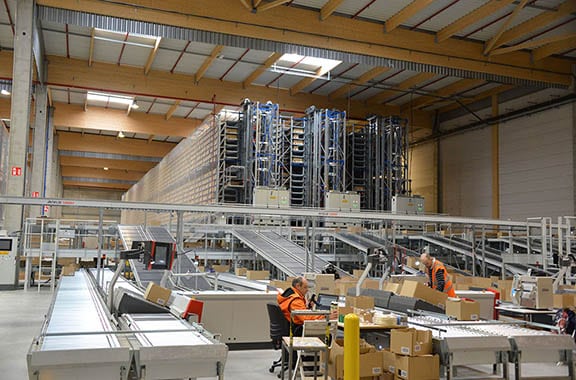
Transporting 600 people by bike over a distance of 600 km (375 miles) is still possible. However, if will be neither quick nor efficient. Conversely, transporting 5 people by plane over a distance of 200 km (125 miles) is quick and efficient, but certainly not very profitable.
The aim of comparing systems is to succeed in achieving a favorable outcome for these 3 aspects: speed, efficiency and profitability. As we have seen, there are several different technologies on the market, each with their own advantages in terms of responsiveness, volume optimization, number of product references to be processed and the number of order lines to be produced.
When carrying out consultations to purchase this type of solution, the operator or the consulting firm providing assistance must ensure that their selection is aligned with rational assessment criteria, ensuring that the solution is adequate for the business activity, but especially the ROI of the system.
Goods-to-Person systems: how to compare them efficiently?
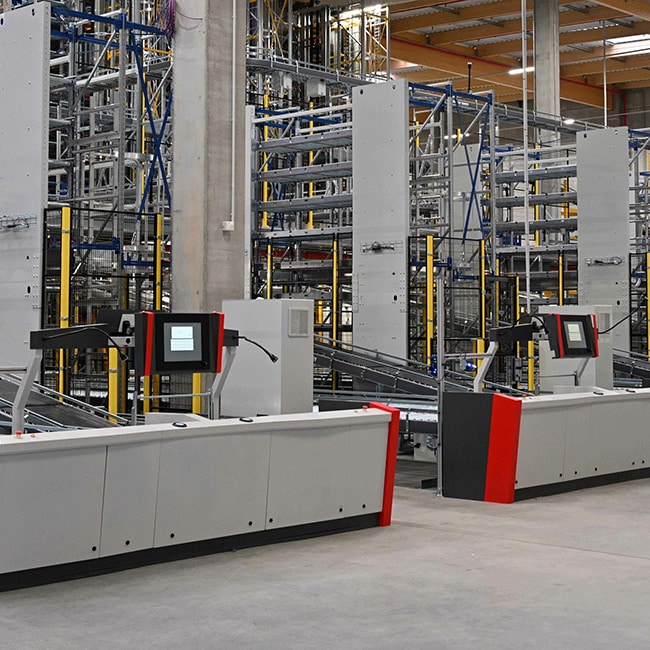